Australian metallic 3D printer producer SPEE3D has introduced the profitable completion of its participation within the Rim of the Pacific (RIMPAC) maritime army train.
SPEE3D deployed its Expeditionary Manufacturing Unit (EMU) in Trident Warrior, the experimental portion of RIMPAC, on the US Marine Corps Air Station in Kaneohe Bay, Hawaii.
The corporate 3D printed 11 cast-equivalent metallic elements from aluminum and chrome steel, leveraging its chilly spray additive manufacturing (CSAM) and post-processing expertise. The fabric properties of those restore and alternative elements will now be studied to evaluate the EMU’s viability for sustaining protection tools in contested environments.
The United States Navy was a significant adopter of additive manufacturing on the train. In response to Byron Kennedy, CEO of SPEE3D, RIMPAC is “the biggest distributed superior manufacturing demonstration the Division of Protection (DoD) has ever carried out to this point.”
He added that the US DoD shares the agency’s objectives to coach the army in 3D printing and implement additive manufacturing. Kennedy believes this expertise provides worth in 3D printing “essential metallic elements on the level of must help modernization and warfighter readiness.”
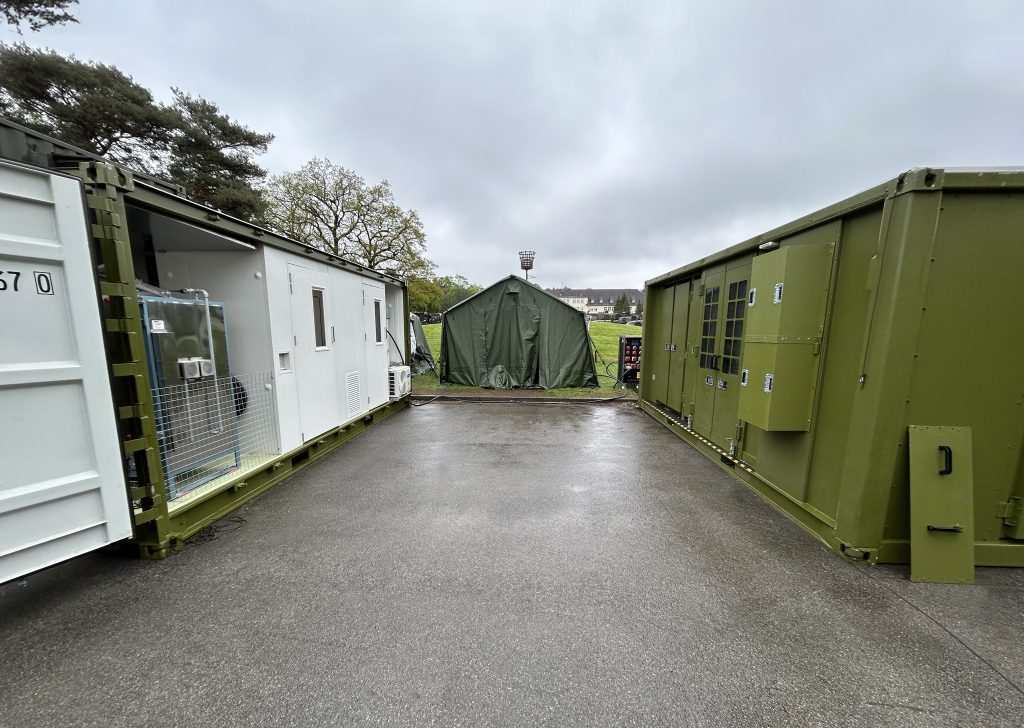
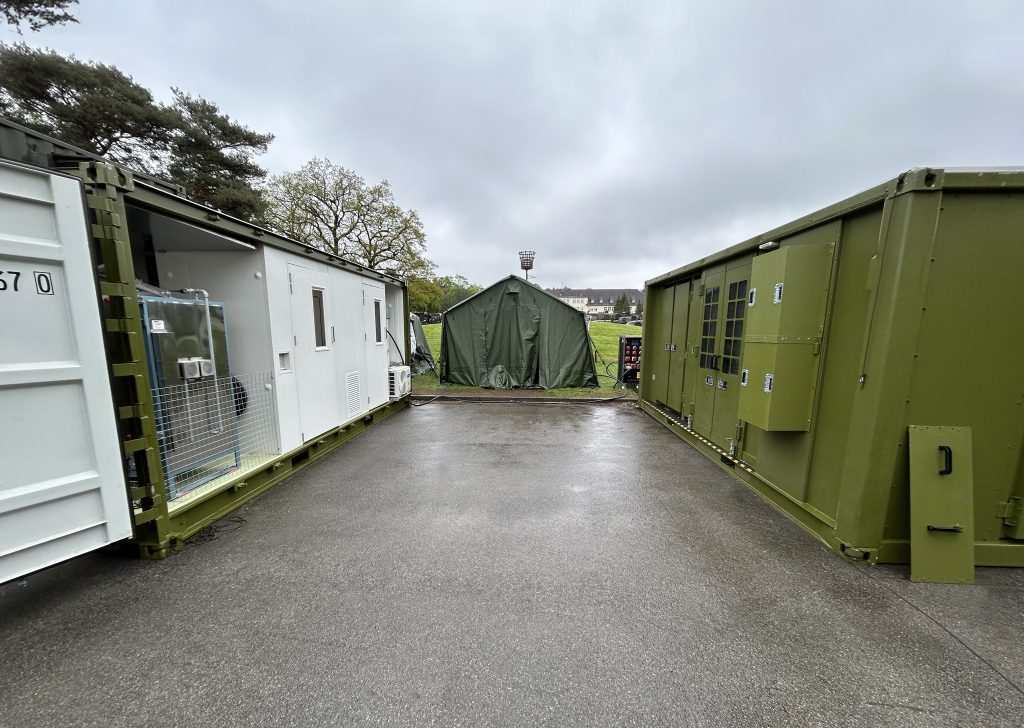
3D printing at RIMPAC 2024
40 ships, 150 plane, three submarines, 14 land-based armed forces and 25,000 personnel from 29 nations participated within the worldwide army train. This reportedly made it the world’s largest world sequence of naval drills.
Throughout Trident Warrior, the EMU was examined by a group of engineers from the US Consortium for Superior Manufacturing Analysis and Training (CAMRE), a part of the Naval Postgraduate Faculty.
Launched earlier this yr, the Expeditionary Manufacturing Unit combines SPEE3D’s XSPEE3D chilly spray 3D printer and SPEE3Dcell post-processing unit. Deployable to distant areas, the containerized system permits army forces to rapidly produce metallic spare elements the place they’re wanted.
By using chilly spray 3D printing, also called Supersonic Particle Deposition (SPD), the XSPEE3D can rapidly fabricate giant and totally dense metallic elements. Boasting a construct fee of 100g/minute, the 3D printer can produce elements as much as ⌀0.9m x 0.7m in dimension. That is reportedly between 100 and 1,000 occasions quicker than different metallic 3D printers available on the market.
The SPEE3Dcell is a fully-equipped cellular post-processing unit that includes warmth therapy furnaces, a CNC three-axis mill, tooling, and testing tools. Warmth therapy is important for manufacturing army spare elements. It ensures 3D printed elements possess good mechanical properties, are sturdy, and may be machined.
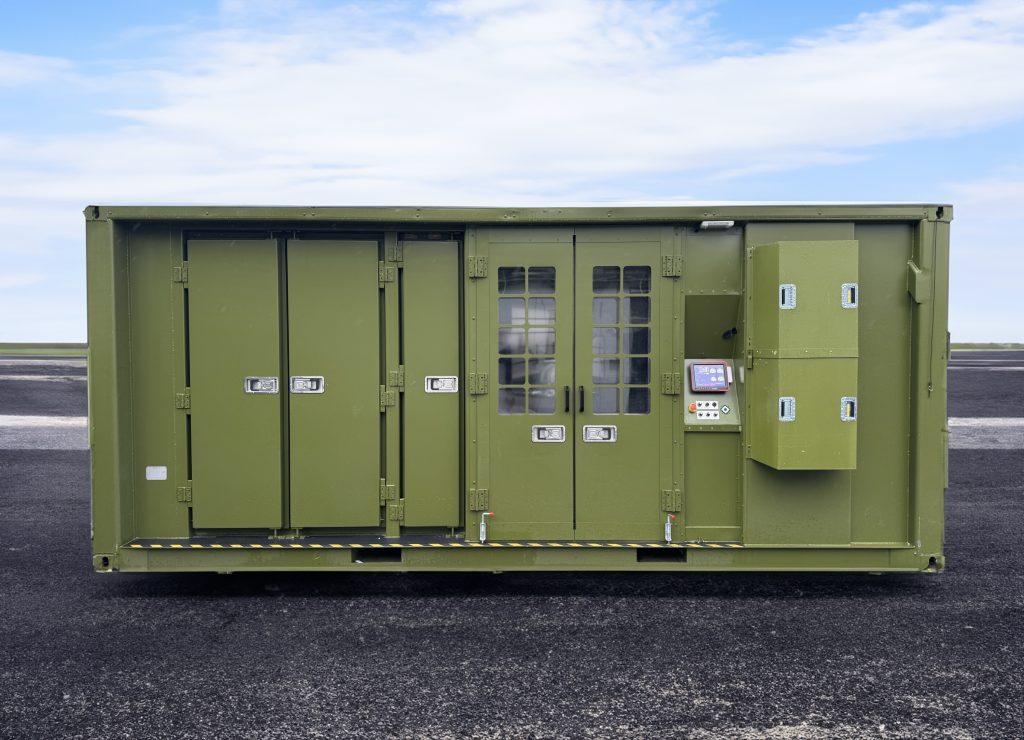
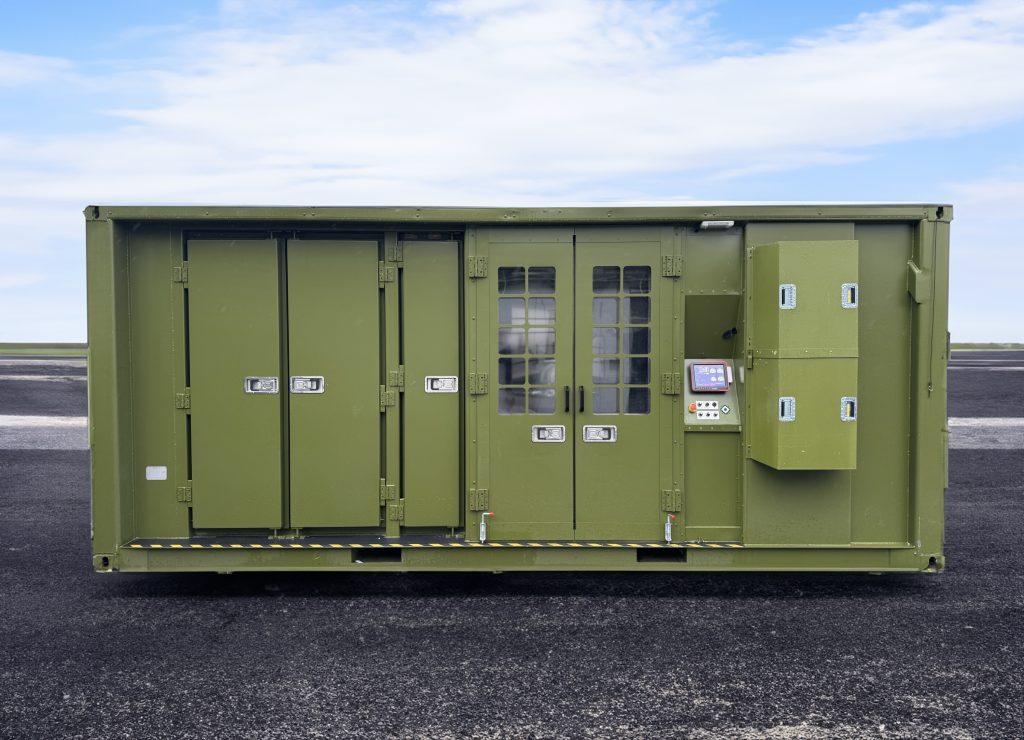
At RIMPAC, CAMRE sought to show that 3D printing can safe army provide chains by lowering the supply time of vital elements from days to hours. Moreover, SPEE3D labored alongside the consortium to uncover greatest practices for 3D printing in expeditionary environments.
The CAMRE group efficiently leveraged the EMU to 3D print 11 cast-equivalent alternative elements for Military, Navy, Air Drive, Marine, and Coast Guard purposes.
Lt. Col. Michael Radigan is a member of the Marine Innovation Unit and was the US Authorities lead on the CAMRE group for Trident Warrior 24. He acknowledged that CAMRE “facilitates getting the most recent in superior manufacturing into operational settings and finds methods to unlock further capabilities.”
Along with the EMU, the US Navy employed Snowbird Applied sciences’ SAMM Tech hybrid DED manufacturing system at RIMPAC 2024. This containerized 3D printer combines Meltio’s metallic wire-directed vitality deposition (DED) expertise with a FANUC-controlled CNC system. As such, metallic elements may be 3D printed, milled and completed on the identical machine.
Through the train, the hybrid manufacturing platform was put in aboard USS Somerset (LPD-25), a San Antonio-class amphibious transport dock.


Additive manufacturing enhances warfighting capabilities
Militaries around the globe are more and more leveraging additive managing to boost the supply of vital warfighting tools
Certainly, RIMPAC 2024 was not the primary time the US DoD has adopted additive manufacturing. Earlier this yr, the US Navy contracted rocket engine producer Ursa Main to design, manufacture and hot-fire check a 3D printed strong rocket motor (SRM) prototype for its Normal Missile (SM) program.
The corporate is leveraging its additive manufacturing-powered Lynx expertise to develop a brand new era of SRMs optimized for manufacturability and reliability. It’s hoped that this may permit the US to satisfy the rising demand for SRMs because it restocks its home inventories and helps Ukraine’s ongoing conflict efforts.
Elsewhere, the British Military 3D printed spare elements within the area for the primary time. It leveraged metallic and polymer 3D printers at Steadfast Defender, NATO’s largest army train for the reason that Chilly Battle.
9 Theatre Assist Battalion, Royal Electrical and Mechanical Engineers (9 REME) leveraged the 3D printers to switch broken or lacking elements for outdated automobiles, comparable to Land Rovers. These included jerry cans, brackets for communications methods, and mounts discovered inside engine bays.
On the metallic aspect, the British Military employed an XSPEE3D unit which it bought final yr. An unnamed FDM 3D printer, or “polymer maker house system,” was additionally used. This was positioned on the again of a lorry, permitting it to be transported to the purpose of want.
Need to assist choose the winners of the 2024 3D Printing Business Awards? Be a part of the Skilled Committee at present.
What does the way forward for 3D printing maintain?
What near-term 3D printing developments have been highlighted by business consultants?
Subscribe to the 3D Printing Business e-newsletter to maintain updated with the most recent 3D printing information.
You may also observe us on Twitter, like our Fb web page, and subscribe to the 3D Printing Business Youtube channel to entry extra unique content material.
Featured picture reveals members of the CAMRE group with the XSPEE3D 3D printer at RIMPAC. Photograph through the Naval Postgraduate Faculty.