A growth of 5 3D-printed houses referred to as Corduroy Castles is at present beneath development in Olivehurst, California, a rural city in Yuba County positioned 40 miles north of Sacramento. The houses will be accomplished in as little as six weeks, in comparison with conventional wood-frame development that may take years. SQ4D manufactured the 3D-printing gear and offered coaching to developer 4Dify, whereas Endemic Structure designed the mission.
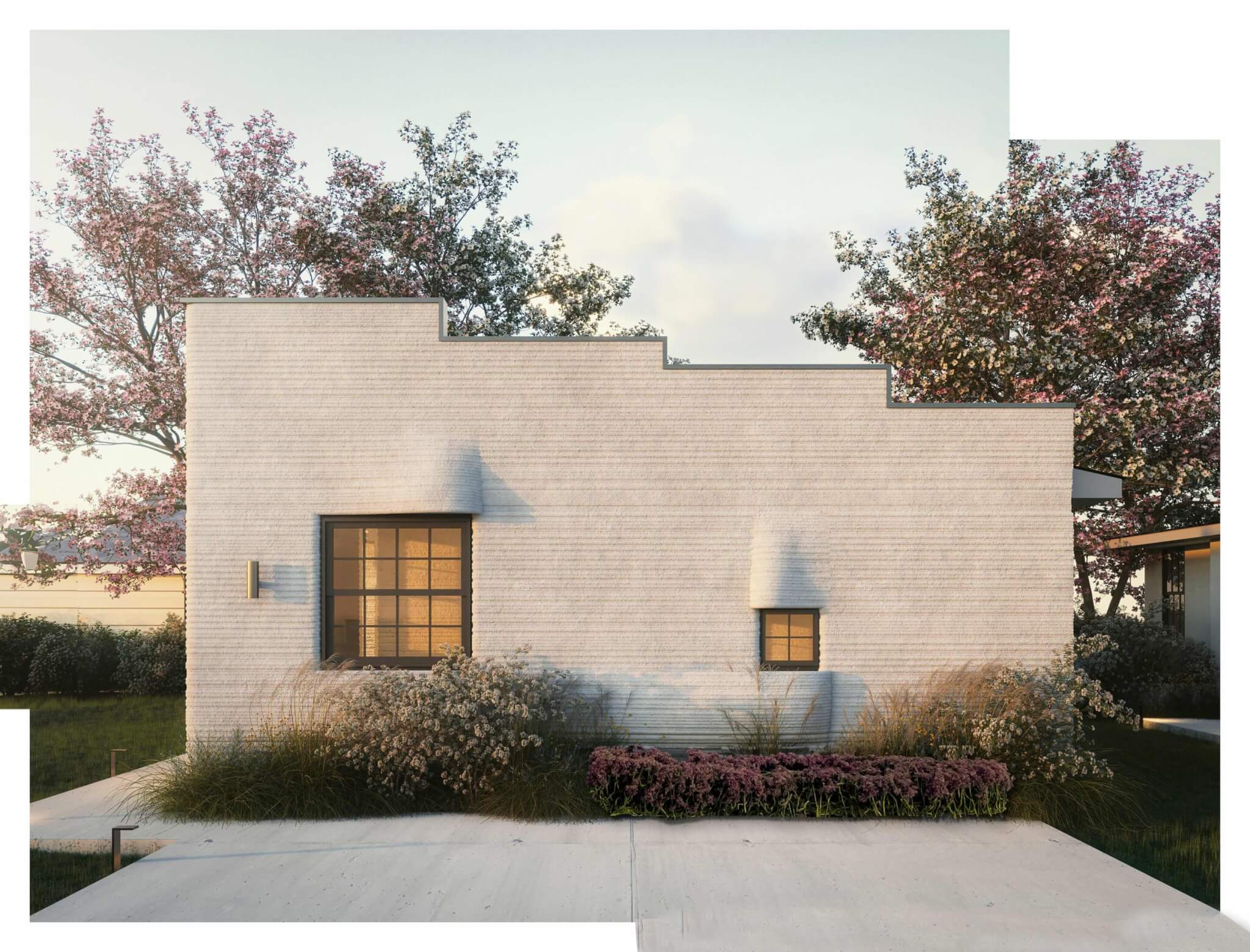
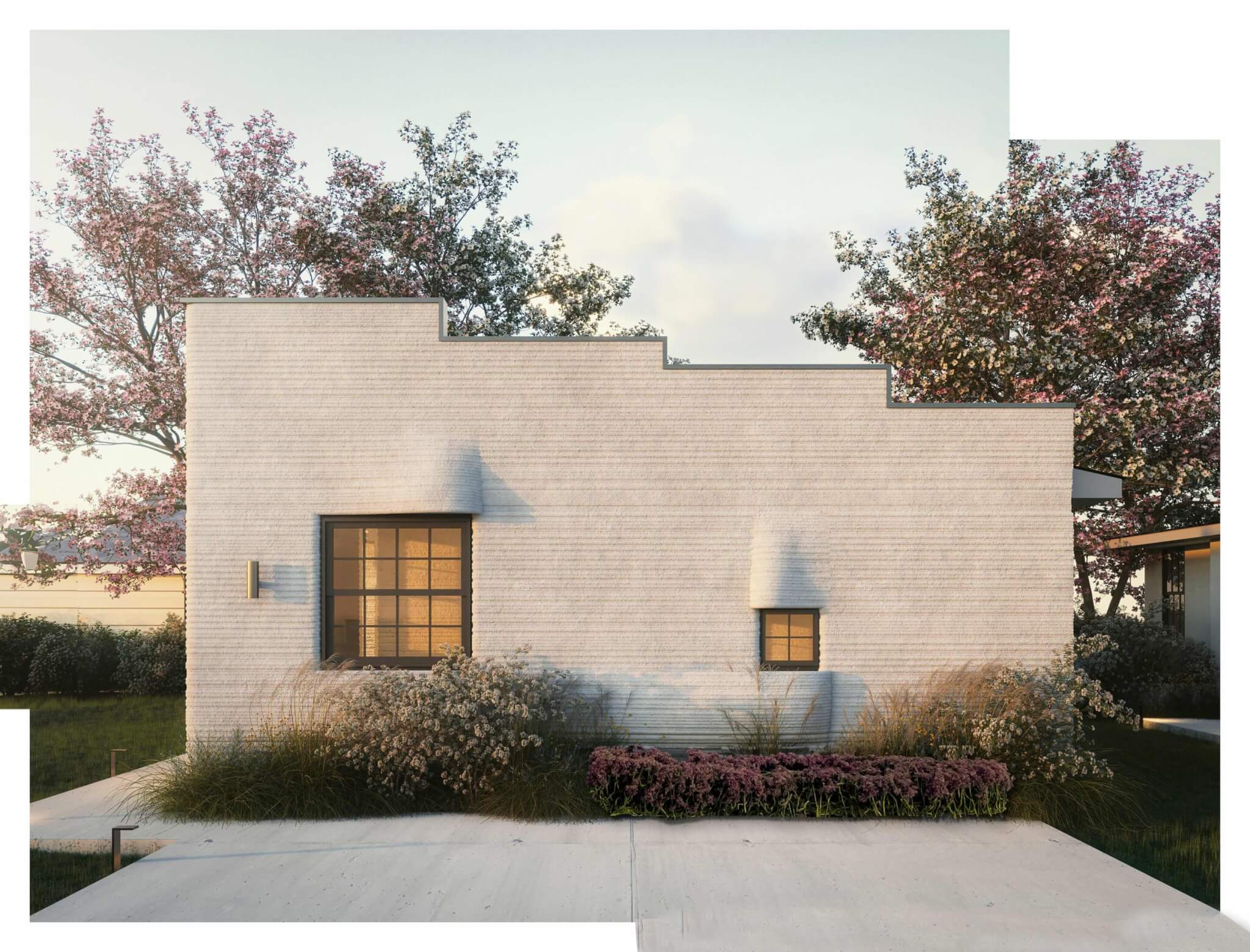
The 980-square-foot houses function three bedrooms and two bogs, with sufficient area for a kitchen island. Every residence consists of carports fairly than garages, with residents coming into by means of facet entrances. The buildings are deliberate to promote beneath market fee, with the time and materials financial savings from 3D printing being handed on to consumers.
Endemic Structure founder Clark Thenhaus describes the event as a “micro-development” method, contrasting it with bigger 3D-printed housing tasks. “The micro-development method feels extra delicate and site-dependent by combining a small lot/infill densification mentality with an current rural group setting as little household castles,” Thenhaus stated. The design consists of distinctive hooded home windows that reference conventional shingle-style structure whereas using the 3D printer’s layering capabilities.
The mission is a part of Sure to Yuba, a county-wide initiative targeted on group growth by means of enterprise innovation and financial progress. Endemic Structure and 4Dify plan extra collaborations within the area on undeveloped properties that require infrastructure enhancements and lot subdivisions. The 3D-printed buildings supply enhanced hearth resistance in comparison with conventional development strategies.
Supply: archpaper.com